Process analysis of CNC machining parts
source: 未知 : 业佳精密 Views: Time:Feb 29, 2024
Description:
The process analysis of CNC machining covers a wide range of areas, so here we only analyze the possibility and convenience of CNC machining. The dimensional data on the parts drawing should comply with the principle of convenient programmi
The process analysis of CNC machining covers a wide range of areas, so here we only analyze the possibility and convenience of CNC machining.
The dimensional data on the parts drawing should comply with the principle of convenient programming
1. The dimensioning method on the part drawing should adapt to the characteristics of CNC machining.
In drawings of CNC machined parts, dimensions should be quoted on the same datum or coordinate dimensions should be given directly. This marking method not only facilitates programming, but also facilitates coordination between dimensions, and brings great convenience to maintaining the consistency of design benchmarks, process benchmarks, inspection benchmarks and programming origin settings. Since part designers generally consider assembly and other usage characteristics when marking dimensions, they have to use partially dispersed marking methods, which will bring a lot of inconvenience to process arrangements and CNC processing. Due to the high precision of CNC machining and repeated positioning, the use characteristics will not be damaged due to large accumulated errors. Therefore, the local scattered annotation method can be changed to an annotation method of the same reference citation size or directly giving the coordinate size. .
2. The geometric element conditions that constitute the part outline must be sufficient
When programming manually, the base point or node coordinates need to be calculated. During automatic programming, all geometric elements that make up the part contour must be defined. Therefore, when analyzing the part drawing, it is necessary to analyze whether the given geometric element conditions are sufficient. For example, arcs and straight lines, arcs and arcs are tangent on the drawing, but according to the dimensions given on the drawing, when the tangent conditions are calculated, they become intersecting or separated. Programming cannot be started due to insufficient component geometry conditions. In this case, you should consult with the part designer to resolve the issue.
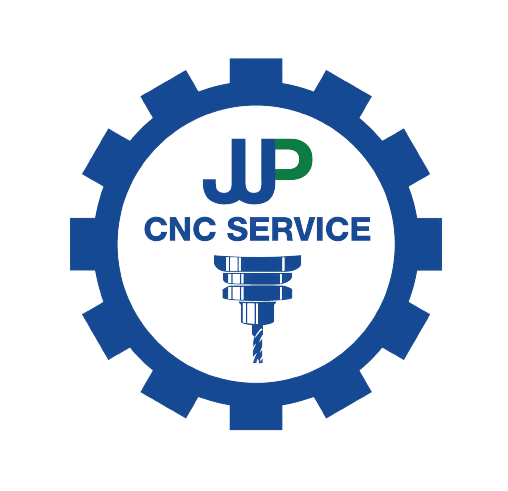